Diversità e miglioramento continuo
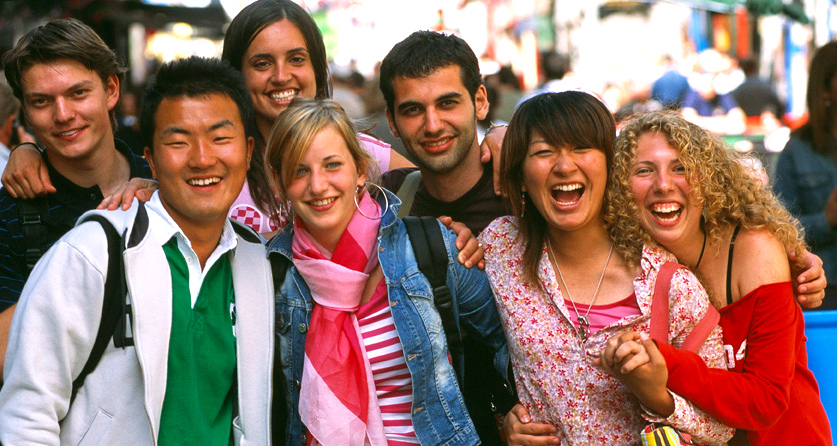
Il Miglioramento Continuo è un linguaggio universale che unisce le diversità in azienda ed aumenta la sicurezza
di Mauro Cogo
Nel contesto socio-economico attuale le aziende ricorrono molto spesso a manodopera a basso costo, introducendo nella loro realtà un’ulteriore difficoltà da affrontare, le differenze culturali e linguistiche.
Specialmente nei settori industriali, dove il time to market, il costo del prodotto e la qualità diventano fattori competitivi fondamentali, le diversità culturali vanno gestite nel modo migliore, soprattutto la formazione ai fini della Qualità, Produttività e Sicurezza. Un addetto straniero ha oggettivamente delle difficoltà di inserimento e quindi è un soggetto maggiormente esposto al rischio.
Apparentemente i temi suddetti non hanno nulla a che vedere con i concetti di Miglioramento Continuo, Lean Thinking e KAIZEN, WCM (World Class Manufacturing), invece non è proprio così, soprattutto se si pensa alla vera essenza di questi metodi, basati sullo sviluppo delle persone e della loro capacità di contribuire ai risultati dell’azienda in un’ottica di miglioramento.
Innanzitutto, quando si parla di lavoro in Team, si parla di capacità di ascoltare, di dialogare a tutti i livelli, dando valore anche alle idee più strane e provenienti da persone che sono apparentemente estranee al processo/prodotto in oggetto; in particolare, agendo in tal senso, si riescono a superare proprio quei paradigmi che oggi sono il freno maggiore al miglioramento e all’innovazione.
Condividere ed applicare un metodo crea una fonte infinita di spunti per il miglioramento dell’ambiente di lavoro, soprattutto perché è il lavoratore stesso che analizza il proprio rischio/problema.
L’applicazione diffusa dei metodi suddetti, sviluppati principalmente da Toyota (Toyota Production System, Toyota Way), crea i presupposti ideali affinché non solo si ottenga un lavoro efficace anche in Team non omogenei, ma soprattutto un modo di organizzare l’ambiente di lavoro e comunicare che appiattisca le differenze, ottenendo anche risultati imprevisti in Produttività e Sicurezza.
In poche parole la diversità, vista generalmente come un problema, può diventare una grande opportunità di miglioramento, la cosa importante è saper “vedere”, superando i paradigmi che ci frenano.
In che cosa consiste l’applicazione del metodo giapponese: semplicemente imparare a “vedere” e non solo guardare, vedere ciò che ha veramente valore per il cliente interno ed esterno e rendere l’ambiente di lavoro semplice, immediato, chiaro anche ai non esperti.
In pratica si sta dicendo che se alleniamo tutti gli operatori a vedere, l’azienda ha una percentuale di probabilità di riscontrare i rischi effettivi molto più alta e quindi le informazioni corrette per ridurli al minimo.
La storia ci insegna che il metodo più efficace al mondo per insegnare, che ha permesso agli Stati Uniti di vincere la seconda guerra mondiale, si basa prima di tutto sul rendere il luogo di lavoro sicuro, facile da imparare, sviluppato direttamente dagli operatori, poi si concentra sull’insegnamento delle operazioni; quindi prima una “bella pulizia consapevole” (pulizia intesa come “un posto per ogni cosa, ogni cosa al suo posto”, ottenendo il massimo dei risultati col minimo rischio).
Se si immagina una strada percorsa da milioni di auto senza segnaletica orizzontale, senza cartelli e senza una corretta istruzione agli automobilisti, cosa succederebbe?
Ecco che gli stessi incidenti possono verificarsi nelle nostre realtà industriali dove il processo non è altrettanto “a prova di errore”; se si vuole fare un test sulla situazione aziendale, basta chiamare un parente/amico che non ha mai visto la vostra realtà e chiedergli di produrre come se fosse lì da anni, possibile senza rischi o spiegazioni? No di sicuro!
Una volta che queste barriere saranno superate le differenze culturali, linguistiche o esperienziali non saranno più un problema.
Concludo citando un esempio pratico:
In una carpenteria un serio problema era il riempimento ottimizzato di un forno di asciugatura dopo la verniciatura; i due operai addetti alla verniciatura non parlavano italiano ed il loro responsabile non sapeva più come fare per spiegare loro cosa fare (caricare il forno alla massima capienza senza ribaltamenti del materiale) e finiva per farlo lui la sera, correndo e facendo da solo manovre non proprio opportune col muletto.
Un giorno, il solito responsabile osservò per caso alcuni gesti del figlio di pochi mesi mentre giocava e si accorse che per rispondere correttamente alle domande dei genitori metteva a confronto forme o colori.
Il giorno successivo disegnò a terra 4 linee che rappresentavano la forma in scala 1:1 del forno in modo che prima di infornare si posizionassero lì i pezzi da verniciare, in questo modo i due operai riuscirono non solo a capire in anticipo come mettere movimentare in sicurezza nel forno il materiale, ma riuscirono a trovare soluzioni diverse che migliorarono il risultato finale.
Da quel momento la lingua non fu più un problema ma un’opportunità.
Non resta che augurare a tutti di intraprendere un processo di riscoperta delle opportunità nascoste per ottenere maggiore Sicurezza, Qualità e Produttività con le stesse risorse.